- Home
- Restoration Articles
- The Dura-Torque Axle
The Dura-Torque Axle
- By Andy Rogozinski
- Published 04/15/2009
- Restoration Articles
Andy Rogozinski

Since 1966 Airstream enthusiasts, movie stars and film crews have depended on Inland RV Center for renovations, expertise, creativity and innovation.
View all articles by Andy Rogozinski
Airstream uses a unique independent suspension system that is contained within the axle tube. The simple compact design gives unparalleled performance compared with other suspension systems.
In 1961, Airstream switched it's suspension system from leaf springs to a rubber torsion principle. The natural cushioning of the special blend of synthetic and natural rubber cords and their self-dampening characteristics made the Henschen axle and the Airstream trailer a perfect match. Each wheel is completely independent . This provides excellent road-handling characteristics. Because the inner torsion shaft is "cradled" in rubber, the axle is extremely quiet. Road noise is completely absorbed by the rubber cords.
To achieve this, the cords are placed in deforming molds and brought down to a temperature of 200 degrees below zero Fahrenheit for two minutes. The deformed rods are then removed from the molds. They retain their "deformed shape" for 30 to 45 seconds, because of the extreme cold that they were subjected to. During this very short time, the rods must be placed in position within the axle. Within less than one minute, the axle is completed because as the rubber compound returns to its original temperature, it also attempts to return to its original shape. However, it cannot return because it is restricted by the inner torsion bar and the outer axle tube. The rubber compound is held to the restricted shape, and serves as four "cushion ride" bearings. As the load is applied, the cushion rods are progressively compressed in a rotating action, which gives the ability to absorb road shock. The axle does not need any maintenance or service.
When coupled with "horizontal type shock absorbers" a ride is achieved that's without equal. However, to enhance this "ride" the tires, wheels, hub and drums must be balanced as an assembly. As with anything that revolves, a high frequency vibration can occur. This high frequency vibration, if not corrected, can be damaging.
To "not" balance the tire, wheel, hub and drum assembly on an Airstream trailer, can cause rivets to shear, sheet metal fatigue, broken wires, water leaks, chassis failure, rear end separation, tire blow outs and excessive tire wear, among other things.
The strength in design is within the axle itself. Each axle has two brackets, one welded near each end of the axle tube where the axle is bolted to the frame. It serves as another cross member, and therefore, retards frame twisting. The axle mounting plates are welded to each side of the frame, and become an integral part of it. This allows weight reduction of the frame and material costs. The mounting plates put additional strength in the frame at the axles.
The installation is simple, four bolts hold each axle in place. Alignment is automatic because of the placement of the mounting holes in the mounting plate.
Along with the advantage of being proven over time, and subject to tough quality standards, an improvement was made in the rods beginning with Airstream's 1974 models.
Research and age showed that the original rubber composition of the rods, could on occasion, lose its resiliency. This would allow the trailer to settle to a lower ground clearance and ball height.
The torsion arm of the axle was set at a 20 to 25 degree positive angle, at "no" load, with a "maximum" travel of 42.5 degrees. As the load increases, this angle can approach zero degrees on up to a negative degree. Positive is downward from the frame, zero is parallel, and negative is upward to the frame.
The axle has build-in torsion arm stops. The stops restrict the negative and positive angles that the torsion arm can achieve, so that the rubber rods cannot be displaced. The downward angle stop allows considerable ground clearance, when a tire and wheel is removed. This allows, with a tandem or tri-axle Airstream, because of the independent wheel suspension, limited continuation of your trip to a tire repair facility. The upper or negative stop prevents the tires from damaging the wheel wells when traveling.
It is wise, especially on pre-1974 Airstream or Argosy trailers, to visually inspect the position of the "torsion arms." This can be done by simple looking rearward from the forward and backside of the front wheel or wheels. As the torsion arm goes rearward, it should have a positive angle (downward). This angle will be greater when the coach is empty, and somewhat less when the coach is heavily loaded.
Each axle has a maximum weight rating. When the trailer is loaded to the maximum weight rating, the torsion arms should still maintain a rearward slight positive or downward angle, but never more than a zero angle (parallel to the frame). Should this rearward angle be negative (upward), then the trailer is overloaded, or the rubber rods have lost some of its resiliency. A negative torsion arm angle will result in the trailer "bottoming out" when hitting bumps. At this point, there is no cushion left, except a small amount provided by the tires.
Another test is to jack up one side of the trailer. The tire or tires should drop at least 3 inches. If not, then the rubber rods have solidified. When the rods have solidified, the cushioning of the axle becomes nil, which causes the trailer to bottom out, when hitting bumps. The "bottoming out" condition places very high loads on tires and can cause tire side wall failure. Additionally, shell and frame damage usually occurs, along with rapid "rear end separation," (the frame separating from the shell at rear of the coach). It can also cause many other types of damages, such as to the furniture, bulkheads pushed away from the shell, among other things.
Should it be found that the axle or axles have a negative torsion arm angle, they should be replaced, to protect your trailer. At the same time the brake system and hub and drums should also be replaced, as some parts for the original brakes are "no longer available".
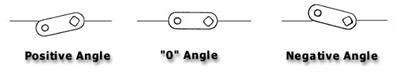
New type electric brakes use oval magnets, instead of the old style round magnets. This in part has added to the braking efficiency. The oval type brakes have a much greater stopping ability than the old style round magnet type brakes.
Henschen "WILL NOT" rebuild any axle. When replacing axles, a rating increase of not more than ten percent, per axle, can be made at little to no additional cost. This is also an excellent time to access the tires and wheels on the trailer. Larger trailers, from 27 feet and up, for added safety, should use 8 ply or load range "D" tires, that are "TRAILER SERVICE RATED," such as Goodyear Marathons. However, if 6 ply tires were in service on the trailer steel wheels, for an extended period of time, upgrading to 8 ply should "NOT" be done. These steel wheels can develop circumference cracks, because of the new and heavier loads impressed upon them, if load range 'D" tires were installed. This does not apply to "mag" wheels.
Replacement wheels must be rated at 2600 pounds, each. Automotive wheels, such as Ford and Chevrolet, "DO NOT" have an adequate rating, and should never be used on any Airstream trailer, not even as a "spare." With proper axles, and running gear properly balanced, an Airstream trailer will tow extremely well, with no equal.
The question of safety should never be compromised. Towing an Airstream trailer can be a joy or an unpleasant experience. The choice is yours.
"And So It Is."
Andy Rogozinski
Inland RV Center, Inc
Corona, CA
In 1961, Airstream switched it's suspension system from leaf springs to a rubber torsion principle. The natural cushioning of the special blend of synthetic and natural rubber cords and their self-dampening characteristics made the Henschen axle and the Airstream trailer a perfect match. Each wheel is completely independent . This provides excellent road-handling characteristics. Because the inner torsion shaft is "cradled" in rubber, the axle is extremely quiet. Road noise is completely absorbed by the rubber cords.
To achieve this, the cords are placed in deforming molds and brought down to a temperature of 200 degrees below zero Fahrenheit for two minutes. The deformed rods are then removed from the molds. They retain their "deformed shape" for 30 to 45 seconds, because of the extreme cold that they were subjected to. During this very short time, the rods must be placed in position within the axle. Within less than one minute, the axle is completed because as the rubber compound returns to its original temperature, it also attempts to return to its original shape. However, it cannot return because it is restricted by the inner torsion bar and the outer axle tube. The rubber compound is held to the restricted shape, and serves as four "cushion ride" bearings. As the load is applied, the cushion rods are progressively compressed in a rotating action, which gives the ability to absorb road shock. The axle does not need any maintenance or service.
When coupled with "horizontal type shock absorbers" a ride is achieved that's without equal. However, to enhance this "ride" the tires, wheels, hub and drums must be balanced as an assembly. As with anything that revolves, a high frequency vibration can occur. This high frequency vibration, if not corrected, can be damaging.
To "not" balance the tire, wheel, hub and drum assembly on an Airstream trailer, can cause rivets to shear, sheet metal fatigue, broken wires, water leaks, chassis failure, rear end separation, tire blow outs and excessive tire wear, among other things.
The strength in design is within the axle itself. Each axle has two brackets, one welded near each end of the axle tube where the axle is bolted to the frame. It serves as another cross member, and therefore, retards frame twisting. The axle mounting plates are welded to each side of the frame, and become an integral part of it. This allows weight reduction of the frame and material costs. The mounting plates put additional strength in the frame at the axles.
The installation is simple, four bolts hold each axle in place. Alignment is automatic because of the placement of the mounting holes in the mounting plate.
Along with the advantage of being proven over time, and subject to tough quality standards, an improvement was made in the rods beginning with Airstream's 1974 models.
Research and age showed that the original rubber composition of the rods, could on occasion, lose its resiliency. This would allow the trailer to settle to a lower ground clearance and ball height.
The torsion arm of the axle was set at a 20 to 25 degree positive angle, at "no" load, with a "maximum" travel of 42.5 degrees. As the load increases, this angle can approach zero degrees on up to a negative degree. Positive is downward from the frame, zero is parallel, and negative is upward to the frame.
The axle has build-in torsion arm stops. The stops restrict the negative and positive angles that the torsion arm can achieve, so that the rubber rods cannot be displaced. The downward angle stop allows considerable ground clearance, when a tire and wheel is removed. This allows, with a tandem or tri-axle Airstream, because of the independent wheel suspension, limited continuation of your trip to a tire repair facility. The upper or negative stop prevents the tires from damaging the wheel wells when traveling.
It is wise, especially on pre-1974 Airstream or Argosy trailers, to visually inspect the position of the "torsion arms." This can be done by simple looking rearward from the forward and backside of the front wheel or wheels. As the torsion arm goes rearward, it should have a positive angle (downward). This angle will be greater when the coach is empty, and somewhat less when the coach is heavily loaded.
Each axle has a maximum weight rating. When the trailer is loaded to the maximum weight rating, the torsion arms should still maintain a rearward slight positive or downward angle, but never more than a zero angle (parallel to the frame). Should this rearward angle be negative (upward), then the trailer is overloaded, or the rubber rods have lost some of its resiliency. A negative torsion arm angle will result in the trailer "bottoming out" when hitting bumps. At this point, there is no cushion left, except a small amount provided by the tires.
Another test is to jack up one side of the trailer. The tire or tires should drop at least 3 inches. If not, then the rubber rods have solidified. When the rods have solidified, the cushioning of the axle becomes nil, which causes the trailer to bottom out, when hitting bumps. The "bottoming out" condition places very high loads on tires and can cause tire side wall failure. Additionally, shell and frame damage usually occurs, along with rapid "rear end separation," (the frame separating from the shell at rear of the coach). It can also cause many other types of damages, such as to the furniture, bulkheads pushed away from the shell, among other things.
Should it be found that the axle or axles have a negative torsion arm angle, they should be replaced, to protect your trailer. At the same time the brake system and hub and drums should also be replaced, as some parts for the original brakes are "no longer available".
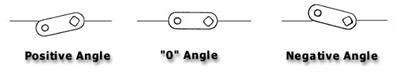
New type electric brakes use oval magnets, instead of the old style round magnets. This in part has added to the braking efficiency. The oval type brakes have a much greater stopping ability than the old style round magnet type brakes.
Henschen "WILL NOT" rebuild any axle. When replacing axles, a rating increase of not more than ten percent, per axle, can be made at little to no additional cost. This is also an excellent time to access the tires and wheels on the trailer. Larger trailers, from 27 feet and up, for added safety, should use 8 ply or load range "D" tires, that are "TRAILER SERVICE RATED," such as Goodyear Marathons. However, if 6 ply tires were in service on the trailer steel wheels, for an extended period of time, upgrading to 8 ply should "NOT" be done. These steel wheels can develop circumference cracks, because of the new and heavier loads impressed upon them, if load range 'D" tires were installed. This does not apply to "mag" wheels.
Replacement wheels must be rated at 2600 pounds, each. Automotive wheels, such as Ford and Chevrolet, "DO NOT" have an adequate rating, and should never be used on any Airstream trailer, not even as a "spare." With proper axles, and running gear properly balanced, an Airstream trailer will tow extremely well, with no equal.
The question of safety should never be compromised. Towing an Airstream trailer can be a joy or an unpleasant experience. The choice is yours.
"And So It Is."
Andy Rogozinski
Inland RV Center, Inc
Corona, CA